摘要:催化裂化裝置在煉油行業(yè)中舉足輕重,產(chǎn)能占比大,其催化劑再生的煙氣是裝置及煉廠的主要污染源;催化原料中含有硫、氮等有害物質(zhì)(硫質(zhì)量分?jǐn)?shù)一般為0.2%~0.7%),隨著渣油摻煉比例的提高,進(jìn)入煙氣中的硫的比例也增大。環(huán)保排放標(biāo)準(zhǔn)越來越嚴(yán)格,煙氣必須脫硫后達(dá)標(biāo)排放,環(huán)保成本增加很大。煙氣濕式堿洗脫硫和硫轉(zhuǎn)移脫硫都能有效降低煙氣中硫的排放,但二者同時(shí)應(yīng)用更具經(jīng)濟(jì)性。
催化裂化是煉油生產(chǎn)中最核心的技術(shù)之一,裂化催化劑再生過程中產(chǎn)生大量煙氣,高溫再生煙氣的主要成分為CO2、CO、N2、O2、SOx、NO2,煙氣中的CO 幾乎全部轉(zhuǎn)化成CO2,最后煙氣排放至大氣,煙氣中還夾帶有催化劑微塵,再生煙氣是催化裂化裝置及煉廠的主要污染源。隨著催化裂化技術(shù)的不斷發(fā)展,催化原料總體趨勢越來越重質(zhì)、劣質(zhì)化。催化原料中的硫根據(jù)工藝技術(shù)( 原料脫硫處理或產(chǎn)品脫硫處理) 的不同其含量差別較大,催化裝置的硫分布也有較大差異,煙氣中的硫總體呈上升趨勢。
隨著環(huán)境保護(hù)標(biāo)準(zhǔn)的提高,煙氣必須進(jìn)行脫硫、脫硝、除塵,實(shí)現(xiàn)達(dá)標(biāo)排放。國內(nèi)外解決煙氣脫硫的技術(shù)路線主要是煙氣濕法堿洗脫硫和硫轉(zhuǎn)移脫硫,因脫硫需要顯著增加成本,朱大亮等對催化裂化煙氣脫硫技術(shù)方案作過比較研究,提出了相關(guān)建議。近年來我國對環(huán)境保護(hù)高度重視,標(biāo)準(zhǔn)高、監(jiān)管嚴(yán),2017 年7 月1 日開始要求排放煙氣中SO2質(zhì)量濃度小于100 mg /m3,與此同時(shí),硫轉(zhuǎn)移助劑的研究和生產(chǎn)又有新的發(fā)展,助劑價(jià)格大幅降低,經(jīng)濟(jì)性也是煉廠關(guān)注的重要課題,因此文章結(jié)合工業(yè)運(yùn)行實(shí)際對二者經(jīng)濟(jì)性進(jìn)行的比較。
1 催化煙氣中硫的存在形態(tài)及含量
催化劑再生過程中硫化物被高溫氧化生成,氧充足環(huán)境下少量生成SO3,因此,硫在煙氣中主要以SO2分子形態(tài)存在,具有較強(qiáng)的腐蝕性,尤其是在露點(diǎn)以下狀態(tài)。
煙氣中硫質(zhì)量濃度高低與原料硫質(zhì)量濃度高低、催化劑性能、裝置結(jié)構(gòu)形式、反應(yīng)條件等因素有關(guān)。以前催化煙氣中硫質(zhì)量分?jǐn)?shù)占原料總硫的5% ~ 15%,但隨著催化原料越來越重質(zhì)化,直餾渣油和加氫渣油摻煉比例的增大,原料中大分子硫化物比例提高,進(jìn)入焦中的硫比例上升,許多裝置超過20%甚至更高達(dá)30%,煙氣中SOx質(zhì)量濃度在500 ~ 3 000 mg /m3,差別較大。
2 煙氣脫硫技術(shù)進(jìn)展
2. 1 煙氣濕法堿洗脫硫
再生煙氣中含有硫氧化物,過高的含量會(huì)不同程度地污染大氣,根據(jù)目前的環(huán)境控制標(biāo)準(zhǔn)必須對煙氣進(jìn)行脫硫處理,普遍采用的有效方法是用NaOH 堿液洗滌,也有使用Mg( OH)2堿液或有機(jī)胺液洗滌吸收,經(jīng)洗滌后的煙氣硫質(zhì)量濃度可降低至50 mg /m3 以下,脫硫率可達(dá)95% 以上。
NaOH 在水中溶解性強(qiáng),又屬于強(qiáng)堿,設(shè)備運(yùn)行可靠性高,堿液運(yùn)輸、儲(chǔ)存方便,反應(yīng)也很充分,洗滌效果好。但缺點(diǎn)是鈉為一價(jià)堿金屬,NaOH消耗量大,運(yùn)行費(fèi)用高。
Mg( OH)2在水中溶解性差,屬于中強(qiáng)堿,因鎂為二價(jià)堿金屬,與NaOH 相比,其消耗量小,運(yùn)行費(fèi)用較低。Mg( OH)產(chǎn)品通常以MgO 于水中,MgO 為固體顆粒,運(yùn)輸和儲(chǔ)存也很方便,堿液和煙氣中硫化物反應(yīng)也很充分,洗滌效果較好。缺點(diǎn)是洗滌液中夾帶有Mg( OH)2微粒,對運(yùn)行系統(tǒng)的設(shè)備磨損嚴(yán)重,設(shè)備運(yùn)行可靠性較差。煙氣濕法堿洗脫硫雖然有效解決了煙氣中SO2的污染問題,但洗滌后的產(chǎn)物為硫酸鹽廢液,大量的硫酸鹽廢液排放又是一個(gè)新的環(huán)保問題。廢液排入大海的沿海煉廠環(huán)保壓力相對較小,內(nèi)地?zé)拸S的排放問題不容小視。硫酸鹽在水中有很高的溶解度并且無毒,但長期排放含鹽、堿性廢水將對當(dāng)?shù)厮w、土壤構(gòu)成危害,一些環(huán)境敏感地區(qū)的環(huán)保部門已正式關(guān)注硫酸鹽的外排問題,要求企業(yè)研究后處理方案,歸根結(jié)底是要找到一條可持續(xù),既不污染大氣也不污染水體還不污染土壤的終極方案。
有多個(gè)解決硫酸鹽技術(shù)方案,如采用膜分離技術(shù),先濃縮硫酸鹽后進(jìn)行干燥,最后制成“鹽餅”等,但無論采用何種方案,都會(huì)增加新的環(huán)保成本。
2. 2 硫轉(zhuǎn)移脫硫
硫轉(zhuǎn)移通常通過助催化劑來實(shí)現(xiàn),把硫化物從再生器轉(zhuǎn)移到反應(yīng)器。硫轉(zhuǎn)移劑采用金屬、稀土作為載體,在催化劑反應(yīng)、再生過程中硫化物被從再生器煙氣中轉(zhuǎn)移到反應(yīng)器油氣中,而且以H2S 的形式存在,硫脫除和回收的場所及方式發(fā)生改變,成本也發(fā)生很大變化,減輕了煙氣洗滌廢水中和所帶來的水污染風(fēng)險(xiǎn)。
國內(nèi)外研究生產(chǎn)了多種硫轉(zhuǎn)移助劑并得到工業(yè)應(yīng)用。硫轉(zhuǎn)移機(jī)理和工業(yè)實(shí)踐表明,助劑在主催化劑中的比例為2% ~ 5%,具體的比例應(yīng)根據(jù)待生催化劑攜帶的硫數(shù)量確定。
根據(jù)反應(yīng)機(jī)理,“貧氧”再生環(huán)境中硫主要被氧化成SO2,SO3很少,助劑難以吸收硫?qū)崿F(xiàn)硫轉(zhuǎn)移,一些硫轉(zhuǎn)移助劑針對“貧氧”再生特點(diǎn)提高助劑中尖晶石氧化鎂活性組分含量,氧化鎂與SO2反應(yīng)形成亞硫酸鹽,實(shí)現(xiàn)硫轉(zhuǎn)移; “富氧”再生環(huán)境具備SO2進(jìn)一步氧化成SO3的條件,SO3與氧化態(tài)金屬形成硫酸鹽從而實(shí)現(xiàn)硫轉(zhuǎn)移,“富氧”環(huán)境利用硫轉(zhuǎn)移助劑能使60% ~ 85% 的硫發(fā)生轉(zhuǎn)移,降低煙氣中SOx質(zhì)量濃度或至達(dá)標(biāo)排放。
對于兩段再生的裝置,進(jìn)入煙氣中的總硫和單段再生接近,因此,可根據(jù)一、二段硫化物的實(shí)際分配調(diào)整硫轉(zhuǎn)移助劑的活性組分比例,保證硫轉(zhuǎn)移效果而不增加硫轉(zhuǎn)移劑成本。
3 硫轉(zhuǎn)移與濕法洗滌技術(shù)和經(jīng)濟(jì)比較
3. 1 技術(shù)路線比較
煙氣濕法堿洗脫硫需要較大的固定資產(chǎn)投資,即新建洗滌塔、堿液配置循環(huán)系統(tǒng)、循環(huán)液過濾系統(tǒng)、廢液中和系統(tǒng)等設(shè)施,技術(shù)上已經(jīng)成熟,煙氣中SOx質(zhì)量濃度可脫至50 mg /m3 以下,脫硫的同時(shí)還可解決煙氣攜帶催化劑粉塵問題,對于煙氣中SOx質(zhì)量濃度大于300 mg /m3 的裝置,為了滿足未來嚴(yán)苛的環(huán)保達(dá)標(biāo)排放標(biāo)準(zhǔn),必須采用濕法堿洗脫硫。因此,濕法堿洗脫硫是絕大多數(shù)催化裂化裝置必須采用的技術(shù)路線。
硫轉(zhuǎn)移脫硫不需要新增后續(xù)固定資產(chǎn)投資,可根據(jù)原料硫及待生催化劑硫的變化靈活使用硫轉(zhuǎn)移劑,對煙氣中SOx質(zhì)量濃度在300 mg /m3 以下的裝置,使用硫轉(zhuǎn)移脫硫是可靠的。煙氣堿液洗滌+ 硫轉(zhuǎn)移同時(shí)使用,二者不產(chǎn)生技術(shù)上的沖突。
硫轉(zhuǎn)移脫硫與濕法堿洗脫硫具有如下差異:
( 1) 脫硫效果差異較大。煙氣堿液洗滌可以實(shí)現(xiàn)深度脫硫,脫后煙氣中硫質(zhì)量濃度可降至接近零,且穩(wěn)定受控。硫轉(zhuǎn)移脫硫不能徹底脫除硫,且脫硫速度低。
( 2) 廢渣及后處理差異大。煙氣堿液洗滌產(chǎn)生亞硫酸鈉、硫酸鈉、硫酸鈉鹽,隨廢水排入江湖、大海,對水體產(chǎn)生不良影響。硫轉(zhuǎn)移脫硫回收硫磺,后續(xù)污染物減少,催化劑有害性不嚴(yán)重,隨主催化劑一起可進(jìn)行掩埋處理。
( 3) 操作控制差異大。煙氣堿液洗滌流程復(fù)雜,設(shè)備多,維護(hù)工作量較大。硫轉(zhuǎn)移脫硫流程簡單、操作簡便,幾乎不需要維護(hù)。
3. 2 經(jīng)濟(jì)性比較
煙氣濕式堿洗脫硫和硫轉(zhuǎn)移脫硫在催化裝置中的工序環(huán)節(jié)不同,煙氣濕式堿洗是在煙氣排放的最后環(huán)節(jié),而硫轉(zhuǎn)移脫硫是在反應(yīng)再生器內(nèi)。硫的去向不同,煙氣濕式堿洗脫硫不回收硫,最后形成硫酸鹽廢水排放; 而硫轉(zhuǎn)移脫硫使硫進(jìn)入產(chǎn)品中,最后回收硫磺。
絕大多數(shù)催化裝置煙氣中的硫質(zhì)量濃度都超過300 mg /m3,需要建設(shè)濕法堿洗脫硫才能保證達(dá)標(biāo)排放的可靠性,因此,在比較二者的經(jīng)濟(jì)性時(shí),就沒有必要考慮濕法堿洗脫硫的固定投資所形成的成本,重點(diǎn)應(yīng)比較二者的運(yùn)行費(fèi)用,運(yùn)行費(fèi)用中除助劑和堿液外,其他能耗和輔助物耗所占比例小,二者相差不大。
某廠一個(gè)實(shí)際加工2. 5 Mt /a 的重油催化裂化裝置,煙氣帶出的硫約3 kt /a,催化劑消耗為1. 4 kg /t 原料,以此為例進(jìn)行實(shí)際核算。
3. 2. 1 煙氣堿洗脫硫
使用質(zhì)量分?jǐn)?shù)45% 的離子膜NaOH 洗滌煙氣,按照2016 年市場價(jià)1 400 元/t,煙氣脫硫堿液的有效利用率94. 4%計(jì)算,中和硫化物耗堿理論費(fèi)用7. 77 元/kg,實(shí)際費(fèi)用為8. 23 元/kg,年耗堿總費(fèi)用約2 450 萬元。運(yùn)行過程消耗電、水、絮凝劑等,年消耗總費(fèi)用約400 萬元。堿液洗滌脫硫項(xiàng)目投資約4 000 萬元。
含硫酸鹽廢水后處理目前國內(nèi)還沒有工業(yè)化裝置,費(fèi)用暫無法測算,有可能會(huì)增加新成本。
3. 2. 2 硫轉(zhuǎn)移劑脫硫
從大多數(shù)催化裝置使用硫轉(zhuǎn)移劑脫硫的實(shí)踐看,硫轉(zhuǎn)移劑在主催化劑中的比例為2% ~ 5%,硫的轉(zhuǎn)移率為60% ~ 85%,硫轉(zhuǎn)移劑的市場價(jià)格近年來有較大幅度的下降( 目前為5. 5 萬元/t) ,如硫轉(zhuǎn)移劑按上限5%加入可滿足脫前煙氣硫氧化物2 500 mg /m3 的要求,硫轉(zhuǎn)移率按65% 計(jì),轉(zhuǎn)移硫消耗硫轉(zhuǎn)移劑費(fèi)用5. 12 元/kg,年總費(fèi)用約1 536 萬元。硫轉(zhuǎn)移脫硫項(xiàng)目投資在100 萬元以內(nèi)。
轉(zhuǎn)移到產(chǎn)品中的硫經(jīng)硫磺回收裝置還原成硫磺,回收加工成本和產(chǎn)品硫磺的市場價(jià)值基本可以相抵。
3. 2. 3 二者經(jīng)濟(jì)性綜合差異
對高含硫煙氣( 煙氣中SO2質(zhì)量濃度超過300 mg /m3 時(shí)) ,為保證環(huán)保達(dá)標(biāo),必須進(jìn)行堿液洗滌脫硫,因此項(xiàng)目投資和運(yùn)行消耗差異可不考慮,而主要考慮脫硫劑( 硫轉(zhuǎn)移劑、堿液) 的成本差。由上所述,二者脫硫成本差為: 8. 23 - 5. 12 =3. 11 元/kg。
對于低含硫煙氣,通過硫轉(zhuǎn)移脫硫可實(shí)現(xiàn)煙氣環(huán)保達(dá)標(biāo),項(xiàng)目投資費(fèi)用更省,二者脫硫成本差更大。
3. 3 技術(shù)經(jīng)濟(jì)綜合比較
兩技術(shù)的綜合差別見表1。
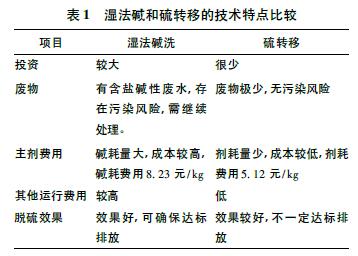
4 結(jié)論
( 1) 采用煙氣濕法堿洗脫硫和硫轉(zhuǎn)移脫硫都能有效降低排放煙氣硫質(zhì)量分?jǐn)?shù)。濕法堿洗技術(shù)對脫前煙氣硫質(zhì)量濃度高低無限制,適應(yīng)性強(qiáng),脫硫徹底( 煙氣中SO2可降至50 mg /m3 以下) ; 硫轉(zhuǎn)移技術(shù)對煙氣硫的脫除率偏低,在新排放標(biāo)準(zhǔn)( 排放煙氣中SO2小于100 mg /m3 ) 下,煙氣脫前硫質(zhì)量濃度低于300 mg /m3,適合采用。
( 2) 硫轉(zhuǎn)移技術(shù)比堿洗脫硫投資和運(yùn)行成本更低,而且沒有二次污染的風(fēng)險(xiǎn); 基于硫轉(zhuǎn)移技術(shù)的硫轉(zhuǎn)移率在60%以上,對煙氣中SO2質(zhì)量濃度低于300 mg /m3 時(shí),可采用硫轉(zhuǎn)移脫硫技術(shù)。
( 3) 鑒于長期運(yùn)行成本的較大差異以及濕法堿洗脫硫的硫酸鹽廢液后處理的技術(shù)難度及運(yùn)行成本,對反- 再系統(tǒng)催化劑循環(huán)量具有彈性的催化裂化裝置,煙氣中SO2質(zhì)量濃度超過300 mg /m3時(shí),應(yīng)該考慮兩項(xiàng)脫硫技術(shù)同時(shí)采用并優(yōu)先采用硫轉(zhuǎn)移脫硫。