近年來隨著勞動力日趨緊缺、勞動成本迅速增加,用地緊張和粘土被禁用,促使制磚技術(shù)不斷進(jìn)步,隧道窯燒磚工藝以大量節(jié)省勞動力和降低工人勞動強(qiáng)度被廣大磚廠所接受,機(jī)器人、碼坯機(jī)代替人工碼坯,大斷面一次碼燒隧道窯生產(chǎn)工藝迅速發(fā)展。窯車運(yùn)轉(zhuǎn)系統(tǒng)聯(lián)動自動化、卸磚自動打包、機(jī)械裝車等裝置被廣泛應(yīng)用,大幅度提高了生產(chǎn)線自動化程度,不僅減少了用工,更重要的是大大降低了工人勞動強(qiáng)度。
從自然干燥、輪窯焙燒到人工干燥隧道窯一次碼燒工藝是一個跨越。但是,不重視專業(yè)設(shè)計(jì),隨意委托沒有設(shè)計(jì)資質(zhì)的窯爐公司自行設(shè)計(jì)建造的隧道窯結(jié)構(gòu)簡單、風(fēng)道設(shè)計(jì)不合理、窯體保溫性能差,造成燒磚能耗偏高、質(zhì)量低劣的現(xiàn)象非常普遍。干燥窯結(jié)構(gòu)不科學(xué)、送風(fēng)方式不合理,導(dǎo)致磚坯干燥效果不佳、干燥過程中嚴(yán)重塌坯倒窯的現(xiàn)象時有發(fā)生。為防止這類事故的繼續(xù)發(fā)生,針對以上問題產(chǎn)生的原因及處理方法談一點(diǎn)體會。
1.1窯體保溫與能耗
燃料成本、電力成本、勞動成本構(gòu)成燒結(jié)產(chǎn)品的三大成本,然而由于建設(shè)不合理、操作不當(dāng)造成燃料浪費(fèi)現(xiàn)象非常普遍。因此,降低能耗是燒結(jié)磚生產(chǎn)線長期的目標(biāo)。
窯體保溫性能優(yōu)劣是降低能耗的關(guān)鍵。常年處于高溫的焙燒窯,大約有30%~40%的熱量被窯體吸收和散發(fā)掉,隨著燃料價格的日趨上漲,提高窯體保溫性能尤其重要。窯體可分為窯墻和窯頂兩個部分。外墻直接與大氣接觸,一般需在墻體內(nèi)增加150px~250px厚度保溫棉以降低熱量損失。窯頂散熱是熱量損失的主要途徑,因此窯頂保溫顯得更為重要,除了在拱頂磚的加層中使用保溫棉之外,還需在上部填充珍珠巖等保溫材料,以增強(qiáng)保溫性能減少熱量損失。常用的硅酸鋁纖維棉、巖棉、珍珠巖、輕質(zhì)保溫磚都是性能良好的保溫材料。在同類地區(qū),窯墻內(nèi)加保溫材料比不加保溫材料燒成1kg制品可以降低能耗50kcal以上。
國家標(biāo)準(zhǔn)規(guī)定窯外墻溫升不超過15℃,窯頂溫升不超過25℃,如果燒磚窯爐能達(dá)到這一標(biāo)準(zhǔn),燒磚能耗就會大大降低。當(dāng)然,要達(dá)到這一要求,窯體就要采用良好的保溫材料。一條4.6m隧道窯約需增加投資10多萬元。
1.2窯車保溫與能耗
窯車散熱也是窯內(nèi)熱量損失的重要途徑,很多隧道窯車底溫度高達(dá)300℃,不但熱量損失嚴(yán)重,還經(jīng)常燒壞軸承。窯車散熱主要是車體砌筑材料保溫性能差和兩車接觸面密封性能差,良好的窯車必須在車底面鋪設(shè)保溫棉、珍珠巖和輕質(zhì)保溫磚,然后再鋪設(shè)耐火磚,接頭處必須采用兩級密封并嵌入保溫棉才能有效減少熱量傳遞到車底。
1.3窯車沙封與能耗
隧道窯沙封密封性能不良不但導(dǎo)致熱量損失,更重要的是導(dǎo)致窯內(nèi)氣流混亂,是出現(xiàn)生磚的主要原因,因?yàn)閺纳撤獯┤氲睦淇諝庵苯幼饔迷诟G車兩側(cè)的磚坯上,窯車兩側(cè)本身由于窯墻吸熱的原因溫度比中部低,再加上冷空氣穿入,溫度就會更低,因此沙封漏氣必定導(dǎo)致窯內(nèi)兩側(cè)出現(xiàn)生磚。
1.4隧道窯通風(fēng)與能耗
燃料燃燒需要足夠的氧氣,空氣中的氧氣是幫助燃料燃燒的介質(zhì),每公斤純碳燃燒大約需要30m3~40m3的空氣。雖然進(jìn)入窯內(nèi)的空氣是靠排煙風(fēng)機(jī)的抽力形成的,但是通風(fēng)道截面積大小是確保通風(fēng)量的關(guān)鍵。沒有足夠的風(fēng)量燃料就不能充分燃燒,每公斤純碳在氧氣充分的條件下燃燒可產(chǎn)生8500kcal熱量,釋放二氧化碳,在氧氣不足的條件下燃料只能產(chǎn)生1700kcal熱量,沒有完全燃燒的碳轉(zhuǎn)變成一氧化碳(煤氣)被排除窯外。
按照每公斤純碳燃燒大約需要30m3~40m3的空氣,每燒1萬塊磚約需1.1t純碳計(jì)算,一條日產(chǎn)20萬塊磚(標(biāo)準(zhǔn)磚)的隧道窯每小時產(chǎn)量約8000多塊, 約需純碳0.88t(880kg),通風(fēng)道每小時需通過880×40=35200m3空氣,按照通風(fēng)道空氣流速8m/s計(jì)算,通風(fēng)道面積應(yīng)達(dá)到35200/3600/8=1.22m2。而通風(fēng)道截面積應(yīng)比計(jì)算面積大1.5倍,因?yàn)闊u所用的內(nèi)燃和外投煤都是純碳,灰分較大,熱值較低,燃燒時需要的氧氣量遠(yuǎn)大于純碳燃燒消耗量。
1.5窯體保溫與磚坯干效果
干燥磚坯的熱量來自焙燒窯的煙熱和余熱。所謂余熱是燒磚過程中磚坯冷卻過程中釋放的熱量,保溫良好的焙燒窯不但燒磚過程中能夠減少熱量損失降低能耗,而且能從冷卻帶抽取足夠的熱量送往干燥窯,確保干燥窯熱量充足,干燥窯有了充足的熱量才能保證磚坯干燥效果。
1.6窯體長度與熱利用率
增加窯體長度不但能提高產(chǎn)量和質(zhì)量,更重要的是提高熱利用率,通過增加窯體長度加長焙燒帶,延長焙燒時間,實(shí)現(xiàn)低溫長燒的焙燒方式。磚坯在相對較低的溫度下延長保溫時間不但能使窯內(nèi)斷面溫度趨于一致,提高制品強(qiáng)度減少生磚,而且在延長焙燒帶的前提下可以適當(dāng)加快進(jìn)車速度能提高產(chǎn)量。更重要的是,加長焙燒窯長度后能夠充分抽取冷卻帶磚坯余熱送往干燥窯干燥磚坯。如果隧道窯長度不足,頂出窯外的磚塊溫度還很高,大量的余熱被散發(fā)在大氣中白白浪費(fèi),只有停留在窯體內(nèi)的磚塊熱量才能被風(fēng)機(jī)抽出送往干燥窯得到利用,因此適當(dāng)增加焙燒長度不斷能提高產(chǎn)量、保證產(chǎn)品質(zhì)量,還能最大限度的利用余熱干燥磚坯。
1.7產(chǎn)量與能耗
由于焙燒窯體所吸收的熱量與時間有關(guān),與產(chǎn)量無關(guān),從年初點(diǎn)火到年底熄火無論燒多少產(chǎn)品窯體每天都在消耗固定的熱量,因此提高焙燒窯日產(chǎn)量是降低能耗的有效途徑。加大焙燒窯通風(fēng)量促進(jìn)燃料快速燃燒是提高產(chǎn)量的必要條件,提高了焙燒窯產(chǎn)量也就相對降低了每塊磚的能耗。
磚坯干燥過程中產(chǎn)生裂紋及倒塌的原因及處理辦法
磚坯干燥過程是坯體從較高環(huán)境溫度中吸收熱量,使坯體中的物理水轉(zhuǎn)變成水蒸氣,受熱氣體隨著溫度升高膨脹,膨脹的氣體壓力升高,較高壓力的氣體就會向壓力較低的自然環(huán)境中釋放,水汽排放需要尋找縫隙從坯體中向外排出。磚坯干燥質(zhì)量是確保燒成質(zhì)量、產(chǎn)量的關(guān)鍵環(huán)節(jié)。沒有理想的干燥磚坯就不能確保焙燒窯的產(chǎn)量和質(zhì)量。結(jié)構(gòu)科學(xué)的干燥窯,合理的送風(fēng)方式、適合原料特性的送風(fēng)溫度,是確保磚坯干燥效果的前提。
增加干燥室容量,降低磚坯升溫速度,延長磚坯干燥周期,提高干燥合格率,才能確保焙燒窯的火行速度,實(shí)現(xiàn)快速焙燒。
2.1影響磚坯干燥性能的三個物理參數(shù)
(1)干燥敏感性——坯體在干燥過程中產(chǎn)生開裂的傾向性。有低、中、高之分,我們把干燥敏感性小于1的原料叫低敏感性,1~2叫中敏感性,大于2叫高敏感性原料。
(2)臨界含水率——坯體在脫去自由水過程中會隨水分減少而收縮,自由水蒸發(fā)而結(jié)束,坯體停止收縮,這時坯體說的含水率成為臨界含水率。隨濕度變化而變化。
(3)塑性指數(shù)——泥料在外力作用下任意改變形狀而不開裂,外力移去后還能保持已改變的形狀。
對于干燥敏感性系數(shù)大于2的高敏感性原料,要求干燥室的長度大于70m,干燥周期應(yīng)在45h以上,送風(fēng)溫度不宜超過120℃,預(yù)熱長度應(yīng)在20m以上,坯體在于熱帶升溫速度控制在3℃/h~4℃/h,于熱帶相對濕度控制在75%~85%,最關(guān)鍵的一點(diǎn)是在成型前加熱原料,提高成型坯體溫度并使坯體內(nèi)溫度趨于一致,并保證成型坯體溫度略高于干燥室進(jìn)口溫度,做到以上條件就能確保磚坯干燥質(zhì)量。
預(yù)熱段空氣濕度大小于取決于原料臨界水分和干燥敏感性,原料臨界水分高,干燥敏感性低,坯體從進(jìn)入干燥室到停止收縮開裂的過程較短,預(yù)熱段低濕度高溫度,可以縮短干燥室長度,實(shí)現(xiàn)快速干燥。反之,干燥室就要相應(yīng)加長,預(yù)熱段就要高濕低溫,降低干燥速度,否則磚坯就會出現(xiàn)裂紋。
2.2碼窯車
碼窯車可以保證燃料和氣流在窯斷面的均勻分配,內(nèi)燃燒磚碼窯車的原則應(yīng)是中細(xì)邊密、底稀上密的碼法,這樣既滿足窯中間間隙大,使潮氣容易流出。實(shí)心磚在干燥過程中反而比空心磚容易塌坯,原因是實(shí)心磚所用原料多,重量大,總水量多,坯體受熱后產(chǎn)生的潮氣量大,如果排潮不足就會導(dǎo)致塌坯。
2.3機(jī)械碼坯
機(jī)械碼坯不但可以保證坯垛的穩(wěn)定性,也能保證坯體之間的間隙一致性。可以認(rèn)為確定邊密中稀并能保證所有窯車碼坯稀密相同一致,便于受熱、通風(fēng)和排潮。目前幾乎所有新建燒結(jié)磚生產(chǎn)線都采用機(jī)械碼坯,因此在確定焙燒窯寬度時必須先根據(jù)磚形設(shè)計(jì)碼車圖,根據(jù)碼車形式確定窯車規(guī)格和焙燒窯有效寬度,且不可隨意確定窯的寬度。
2.4磚坯預(yù)熱
磚坯預(yù)熱過程是坯體由外到內(nèi)的升溫過程,這一過程既要確保坯體緩慢升溫,又要降低磚坯表面脫水速度,這就要保證預(yù)熱帶保持低溫高濕狀態(tài)。因?yàn)榕黧w表面受熱快,坯體表面的水分就會逐漸變成水汽向空氣中擴(kuò)散而被對流的空氣帶走,這時如果坯體周圍空氣相對濕度較小,坯體表面水分就會迅速蒸發(fā),水分蒸發(fā),體積就會減小,表面就會收縮,坯體內(nèi)部溫度還較低,水分不會蒸發(fā),體積也就不變化,內(nèi)外收縮不一致就會造成坯體表面開裂。因此,必須等到坯體內(nèi)部溫度升高到開始蒸發(fā)水分時才能進(jìn)入到脫水階段。要保證坯體表面水汽不被迅速蒸發(fā),就必須保證坯體周圍的空氣濕度。坯體在預(yù)熱段到干燥段這一升溫階段,坯體的空氣濕度應(yīng)保持在70%~80%,溫升速度應(yīng)控制在3℃/h~5℃/h。升溫過快,只會加快坯體表面溫升速度,坯體表面向坯體內(nèi)部的熱傳導(dǎo)升溫速度又相對坯體表面的空氣對流升溫慢得多,在這一緩慢過程中必須讓坯體處在一個高濕的環(huán)境中,也就是坯體的預(yù)熱階段,這個階段一般需要8h~12h,預(yù)熱段長度約20m~25m。如果預(yù)熱階段坯體周圍的空氣濕度較低,就會導(dǎo)致坯體表面脫水速度加快,坯體內(nèi)外脫水速度不一致,使坯體表面開裂。
2.5送風(fēng)量與送風(fēng)壓力
風(fēng)機(jī)變頻器的應(yīng)用方便了風(fēng)機(jī)啟動和靈活調(diào)整。但是,為干燥窯選型的風(fēng)機(jī)不只是為了燒窯而選的。對于一條3m多的隧道窯而言,滿足焙燒只需要一臺每小時排風(fēng)量3萬m3、壓力280pa、功率為7.5kw的風(fēng)機(jī)即可。但是,為了給干燥窯送風(fēng),通常選用壓力1200pa、風(fēng)量在10萬m3、功率在45kw以上的風(fēng)機(jī)。
燒窯工為了滿足燒磚所需的氧氣量隨意降低風(fēng)機(jī)頻率,導(dǎo)致進(jìn)入干燥窯的風(fēng)量風(fēng)壓嚴(yán)重不足是塌坯的主要原因。因?yàn)轱L(fēng)機(jī)的風(fēng)量與轉(zhuǎn)速成1次方關(guān)系,風(fēng)壓與轉(zhuǎn)速成平方關(guān)系,當(dāng)頻率由額定的50赫茲降低到30赫茲時,轉(zhuǎn)速時額定的60%,這時的風(fēng)量是額定的60%,而壓力卻只有額定的36%。小風(fēng)量不能將側(cè)面送入的風(fēng)吹到窯車中間,也不能將頂部送入的風(fēng)吹到車面,就不能使下部磚坯之間形成空氣對流,潮氣就不能排出。
送風(fēng)溫度直接影響到預(yù)熱帶的坯體升溫速度和干燥段脫水速度,所以,對不同的原料和坯體含水率,送風(fēng)溫度應(yīng)不同,一般情況下軟質(zhì)原料的送風(fēng)溫度不要超過110℃。這樣,可以確保坯體在預(yù)熱過程中合理升溫。送風(fēng)溫度過高會導(dǎo)致坯體蒸發(fā)水分過快,會使干燥窯內(nèi)水汽量過大,超過了排潮風(fēng)機(jī)的排風(fēng)量,使預(yù)熱段的相對濕度達(dá)到飽和,就會使磚坯變軟而倒塌。
2.6漏氣造成塌坯
漏氣是導(dǎo)致塌坯的一個主要原因,進(jìn)車端升降門周圍漏氣導(dǎo)致外界冷空氣進(jìn)入干燥窯,造成排潮風(fēng)機(jī)排出潮氣量下降,使高溫潮氣滯留在坯體表面,導(dǎo)致坯體變軟而造成塌坯。現(xiàn)在大多數(shù)干燥窯只設(shè)了一道門,可就是這一道門,很多廠家也不重視門的密封效果,門的四周與端墻之間的底部軌道之間的縫隙很大,甚至門已經(jīng)損壞也不修復(fù),這樣必然降低排潮風(fēng)機(jī)的抽力。
磚坯產(chǎn)生裂紋的主要原因是:(1)干燥窯預(yù)熱段溫度、濕度與原料的臨界水分、干燥敏感性對應(yīng)的環(huán)境不符。(2)環(huán)境溫度低,成型坯體內(nèi)外溫差大,坯體表面水分蒸發(fā)遠(yuǎn)快于內(nèi)部水分蒸發(fā)。(3)擠磚機(jī)壓力小,成型水分高,原料臨界水分低,成型水分與臨界水分差值太大。(4)原料塑性指數(shù)偏高,坯體不易脫水,干燥升溫快,導(dǎo)致坯體表面開裂。
磚坯在干燥過程中出現(xiàn)塌坯是常見現(xiàn)象,尤其是軟質(zhì)原料塌坯倒窯現(xiàn)象更為常見。造成塌坯的原因很多,比如磚坯成型水分偏高,坯體強(qiáng)度低,下部坯體承受不了上部坯體的壓力造成塌坯,坯垛碼放層數(shù)過高使下部坯體被壓變形造成塌坯,坯垛碼放不規(guī)范使得受壓不均造成塌坯。但是送風(fēng)溫度過高、升溫速度過快是造成塌坯的常見原因。總之,降低能耗由多種途徑,提高窯的保溫性能和焙燒窯產(chǎn)量,是降低能耗的有效途徑。
導(dǎo)致干燥窯塌坯的因素很多,有干燥窯結(jié)構(gòu)設(shè)計(jì)方面的因素,也有操作方面的因素,具體問題應(yīng)根據(jù)實(shí)際情況找出問題所在,對癥處理,使問題得到徹底解決。工藝設(shè)計(jì)流暢、窯爐結(jié)構(gòu)設(shè)計(jì)合理、保溫性能良好、施工質(zhì)量優(yōu)良,是降低能耗、提高產(chǎn)品質(zhì)量的關(guān)鍵。
近年來隨著勞動力日趨緊缺、勞動成本迅速增加,用地緊張和粘土被禁用,促使制磚技術(shù)不斷進(jìn)步,隧道窯燒磚工藝以大量節(jié)省勞動力和降低工人勞動強(qiáng)度被廣大磚廠所接受,機(jī)器人、碼坯機(jī)代替人工碼坯,大斷面一次碼燒隧道窯生產(chǎn)工藝迅速發(fā)展。窯車運(yùn)轉(zhuǎn)系統(tǒng)聯(lián)動自動化、卸磚自動打包、機(jī)械裝車等裝置被廣泛應(yīng)用,大幅度提高了生產(chǎn)線自動化程度,不僅減少了用工,更重要的是大大降低了工人勞動強(qiáng)度。
從自然干燥、輪窯焙燒到人工干燥隧道窯一次碼燒工藝是一個跨越。但是,不重視專業(yè)設(shè)計(jì),隨意委托沒有設(shè)計(jì)資質(zhì)的窯爐公司自行設(shè)計(jì)建造的隧道窯結(jié)構(gòu)簡單、風(fēng)道設(shè)計(jì)不合理、窯體保溫性能差,造成燒磚能耗偏高、質(zhì)量低劣的現(xiàn)象非常普遍。干燥窯結(jié)構(gòu)不科學(xué)、送風(fēng)方式不合理,導(dǎo)致磚坯干燥效果不佳、干燥過程中嚴(yán)重塌坯倒窯的現(xiàn)象時有發(fā)生。為防止這類事故的繼續(xù)發(fā)生,針對以上問題產(chǎn)生的原因及處理方法談一點(diǎn)體會。
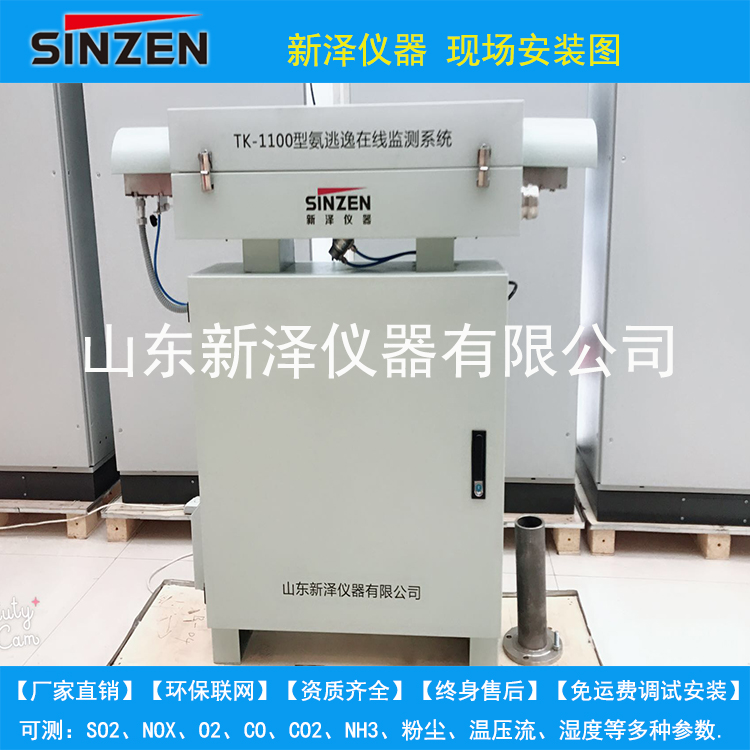
山東東新澤儀器有限公司注冊于山東濟(jì)南市,是一家集氣體分析儀器、環(huán)保監(jiān)測設(shè)備及配套零部件產(chǎn)品研發(fā)、生產(chǎn)、銷售及售后服務(wù)為一體的高科技企業(yè)。
主要產(chǎn)品有氧分析儀系列、露點(diǎn)儀系列、氫氣分析儀系列、紅外線分析儀系列、氣體報警儀系列等,同時過程分析系統(tǒng)有CEMS煙氣連續(xù)監(jiān)測系統(tǒng)、脫硫脫硝煙氣分析系統(tǒng)、在線VOCs分析儀、便攜式VOCs分析儀、窯爐氣體分析系統(tǒng)、冶金行業(yè)氣體分析系統(tǒng)、煤化工分析系統(tǒng)、水泥窯氣體分析系統(tǒng)、焦?fàn)t煤氣氧分析系統(tǒng)、化工行業(yè)氣體分析系統(tǒng)、空分行業(yè)氣體分析系統(tǒng)、化學(xué)制藥氣體分析系統(tǒng)等。
hz